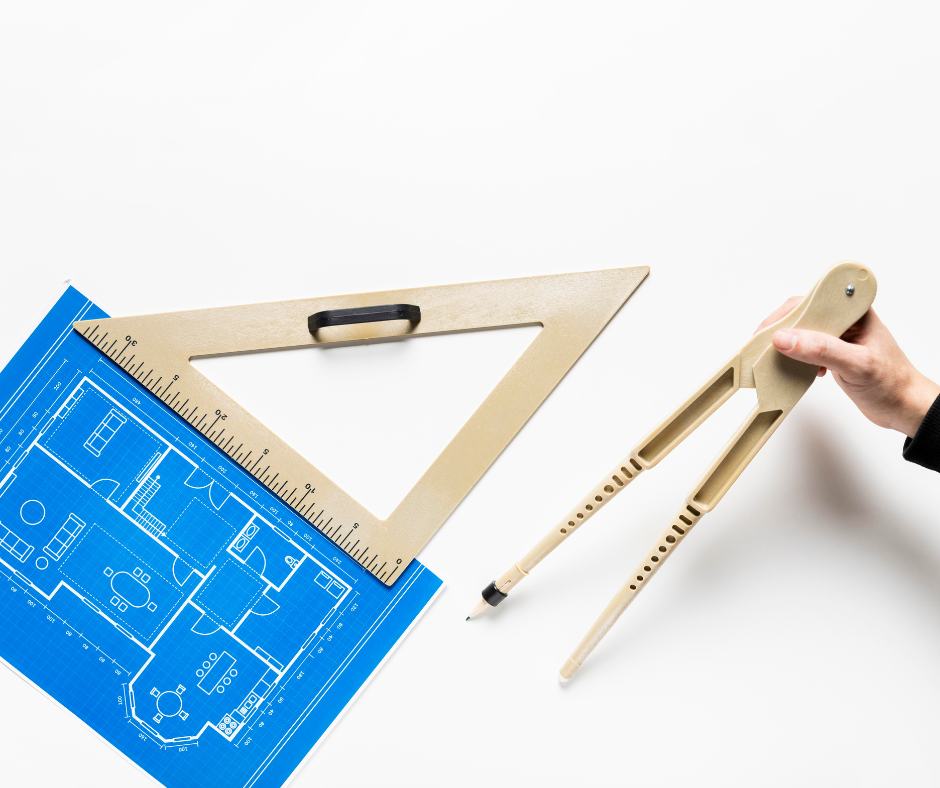
3D Scanning vs Hand Measuring: A Race Against Time
In construction and renovation, accuracy is everything — and time is money. Whether you’re planning a remodel, a commercial buildout, or a historic restoration, your project begins with one essential deliverable: the as-built drawings
For decades, professionals have relied on tape measures, laser distance meters, and clipboards to manually document building conditions. But now, 3D scanning is transforming how we capture site data — delivering high-precision as-built plans in a fraction of the time.
In this article, we break down the key differences between 3D scanning vs hand measuring, and explain why LiDAR technology is quickly becoming the gold standard in as-built documentation.
As-Built Drawings: What They Are and Why You Need Them
As-built drawings show the exact layout and dimensions of a structure as it exists — not just what was designed on paper. These drawings are essential for:
- Renovations and tenant improvements
- Building permits and code compliance
- Clash detection in BIM modeling
- Facility maintenance and space planning
Without accurate as-builts, every phase of a project is vulnerable to error, delays, and budget overruns.
Traditional Hand Measuring: Familiar, but Flawed
Hand measuring has been the default approach for decades. It involves manually recording measurements and sketches onsite — room by room, floor by floor.
Pros:
- Low-tech and accessible
- Familiar to most contractors and designers
- Requires no special equipment
Cons:
- Time-consuming: Even small commercial spaces can take days to measure
- Human error: Missed measurements or illegible notes can compromise accuracy
- Disruption: Occupied buildings may require downtime or limited access
- No digital file: Often requires redrawing or CAD input after the fact
Manual measuring works, but its limitations become painfully clear on larger or more complex jobs.
3D Scanning: Speed Meets Precision
3D scanning for construction projects uses LiDAR (Light Detection and Ranging) to quickly capture spatial data by emitting laser pulses and measuring how they reflect off surfaces.
This creates a point cloud — a 3D digital representation of the structure — that can be converted into as-built drawings, 3D models, or even a full LiDAR scan to BIM service.
Benefits of 3D Scanning:
- ✅ Rapid Data Capture: Entire buildings scanned in hours, not days
- ✅ High Accuracy: Down to millimeter precision
- ✅ No Downtime: Work around building occupants without disruption
- ✅ Comprehensive: Captures everything — even inaccessible areas
- ✅ Digital-Ready: Point cloud can be directly converted to CAD/BIM
A Head-to-Head Comparison: Hand Measuring vs 3D Scanning
Feature | Hand Measuring | 3D Scanning |
---|---|---|
Time Required | Days or weeks | Hours or a single day |
Accuracy | ±1–2 inches | ±1–2 millimeters |
Risk of Human Error | High | Very low |
Output Format | Paper/Manual Notes | CAD/BIM-Ready Digital Models |
Cost (Short-Term) | Low | Medium |
Cost (Long-Term ROI) | High (due to errors) | Lower (fewer errors/rework) |
Usability for Complex Sites | Difficult | Ideal |
For any project involving tight schedules, complex structures, or high standards, 3D scanning wins by a wide margin.
Real-World Applications: When 3D Scanning Saves the Day
1. Commercial Renovations
Scan an entire retail space after hours and begin design work the next morning.
2. Historic Preservation
Capture fragile buildings without physical contact, preserving details for restoration.
3. MEP Coordination
Use precise as-builts to model HVAC, plumbing, and electrical systems without clashes.
4. Multi-Site Portfolios
Standardize documentation across dozens of properties with consistent digital models.
📍 Explore how we deliver high precision as-built plans for Construction and Renovation Projects.
Why Accuracy Matters More Than Ever
The cost of a bad measurement isn’t just a number on paper — it’s lost time, blown budgets, and legal headaches.
- A single missed pipe or structural column can delay permitting.
- An inaccurate ceiling height might require redesign mid-construction.
- Clashes between old conditions and new plans can trigger costly rework.
By contrast, starting with high-accuracy as-built drawings from a 3D scan ensures that every stakeholder — architects, engineers, contractors, and owners — works from the same, reliable truth.
How We Do It at LiDAR Precise Plans
Our 3D scanning process combines advanced terrestrial LiDAR equipment with architectural expertise. Here’s what you get:
- Onsite 3D Laser Scan – Fast, non-intrusive scanning of interiors and exteriors
- Point Cloud Creation – High-resolution model of every surface
- As-Built Documentation – 2D floor plans, elevations, and BIM models
- Internal Linking and Collaboration – Ready-to-use files for designers and GCs
All delivered with accuracy, speed, and support you can trust.
📍 Get in touch for a Custom 3D Scanning Quote.
Conclusion: The Smart Choice is Clear
In the race between hand measuring and 3D scanning, there’s no contest.
Modern construction projects demand speed, precision, and confidence — all of which 3D scanning delivers.
If you’re still using tape measures and paper sketches to begin major projects, it’s time to upgrade.
Start smarter. Build better.
It all begins with the scan.
📍 Let us help you produce accurate, dependable As-Built Drawings — the first step toward a successful project.